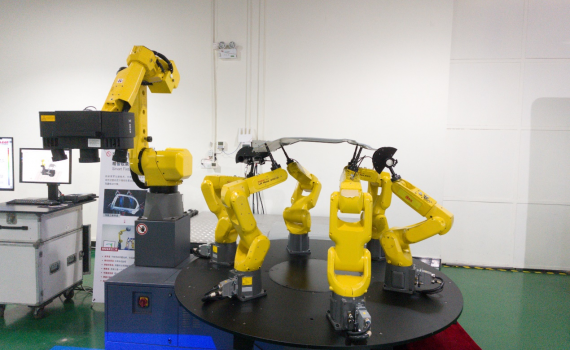
创新变革先进技术 无需真实固定夹具 自然放置状态下模拟计算出虚拟夹紧的3D测量自动化解决方案 省心、省时、省力,大大降低成本 精智锐柔性工装Smart Fixture 传统工装的缺点和劣势: 成本高:设计、生产、校准和存储等环节均需投入大量资金。 修改成本高:一旦数模或夹紧点发生变化,需要重新设计和制造夹具。 测量成本高:测量时需要频繁调整夹紧点,增加了测量时间和难度。 精度有限:不完美的支撑点往往导致测量误差。 重复性有限:人为因素和夹紧顺序的差异会影响测量结果。 测量受限:扫描头可能因夹具的遮挡而无法进行全面测量。 制作周期长:每款新制夹具生产时间长。 精智锐柔性工装Smart Fixture自动化3D检测系统 结合蔡司三维光学测量技术+精智锐柔性机械人 搭载数据分析软件和物联网(loT) 实现自动化全方位扫描 以虚拟计算代替物理夹具 实现多品类钣金工件通用测量 精智锐柔性工装Smart Fixture的优势: 成本低:代替传统测量检具,夹具通用。 修改效率高:无需修改数模。 测量效率高:测量时不需要调整夹紧点,灵活通用。 精度高:支撑点是一个点,精度更高。 可重复使用:柔性通用夹具,无人为影响。 测量不受限:扫描头视野好。 周期短:无需新制夹具,仅需调试时间。 测量原理示意图 宏领智能装备(东莞)有限公司是宝力机械集团全资子公司,致力于为制造企业提供专业、全面的自动化解决方案。精智锐是宏领智能装备(东莞)有限公司自主研发品牌,结合先进的蔡司三维光学测量技术和虚拟装夹先进技术FEM算法,精智锐柔性工装Smart Fixture引领3D测量革命性创新,工业生产制造中各种钣金工件都能通用测量。未来,随着智能制造的不断发展,Smart Fixture将成为更多企业提质增效的检测利器,助力制造业质量控制迈向更加智能化、高效化的新时代。